Tradycyjne techniki w procesie produkcyjnym Manufaktury
Lorem ipsum dolor sit amet, consetetur sadipscing elitr, sed diam nonumy eir mod tempor invidunt ut labore et dolore magna aliquyam erat.
Współczesny przemysł ceramiki stołowej stara się wprowadzać nowe rozwiązania technologiczne. Budowanie ciągów maszynowych daje większe możliwości przerobowe. Maszyny do odlewu ciśnieniowego, piece tunelowe czy roboty wspomagające szkliwienie wyrobów zwiększają wydajność i jakość wytwarzanych produktów. Zależnie od kierunku i polityki firmy rozwiązania te mogą sprzyjać lub nie założeniom produkcyjnym. W fabrykach porcelany na terenie Polski można dostrzec tendencję polityki podwykonawczej. W zestawieniu z kamionką produkt porcelanowy jest dużo tańszy. Wyroby kamionkowe, szczególnie bolesławieckie, ze względu na metodę ręcznej produkcji, są znacznie droższe. Produkcja masowa daje większą przewidywalność i możliwość organizacji pracy, kontroli jakości i usprawnienia ciągu produkcyjnego. Jest częściej wykorzystywana przez fabryki, których polityka sprzedaży opiera się na klientach kontraktowych, zamawiających większe ilości produktów.
Produkcja wyrobów w Manufakturze ze względu na duży wkład pracy ręcznej ma charakter bardzo elastyczny. W krótkim czasie system jest w stanie dostosować się do różnego rodzaju zamówień, nawet z zakresu sprzedaży detalicznej. Zakłady dbające o markę i produkcję opartą na tradycyjnych metodach wytwarzania zachowują w procesie wytwarzania charakterystyczne, ręczne metody formowania lub zdobienia wyrobów. Daje to możliwość trzymania się tradycyjnej ścieżki wprowadzania produktu na rynek, a tym samym utrzymania na odpowiednim poziomie wartości marki w świadomości konsumentów. Cenne jest również to, że przy tak bogatym zapleczu technologicznym i częstym zastępowaniu pracy ludzkich rąk maszynami w wielu zakładach wciąż stosuje się metody i techniki, które odciskają ślad jednostki na powstałym produkcie, podkreślając jego unikatowość. W procesie produkcyjnym Manufaktury część elementów tradycyjnych zastąpiły nowe technologie zwiększające wydajność i dające nowe możliwości. Jednak siłą napędową, niosącą dodatkowe wartości, pozostają metody o charakterze bardziej elastycznym i zmiennym, metody tradycyjnie „ludzkie”.
Tradycyjne sposoby wytwarzania
W Manufakturze trzy metody stanowią dobrą bazę do dyskusji na temat tradycyjnych sposobów wytwarzania bolesławieckich wyrobów kamionkowych. Formowanie naczyń za pomocą toczenia w formach gipsowych na foczkach, odlewania w formach gipsowych oraz przede wszystkim ręczne zdobienie/dekorowanie ceramiki to procesy, przez pryzmat których łatwiej nakreślić obszar działań projektowych ustawionych pod kątem możliwości produkcyjnych.
Formowanie na toczku
Formowanie naczyń na toczkach lub odlewanie w formach gipsowych to metody od lat znane w przemyśle ceramicznym, które wciąż są wykonywane ręcznie. Aby zaformować głębokie naczynia o kształtach cylindrycznych (jak kubki, miski, filiżanki czy garnki), w Manufakturze stosuje się jedno ze starszych rozwiązań: ręczny toczek formierski, w którym napęd przekazywany jest z silnika elektrycznego przez przekładnię pasową oraz sprzęgło cierne (analogicznie jak w samochodzie) do umieszczonego na wspólnej osi stalowego gniazda, w którym umieszcza się formy gipsowe.
Formę gipsową, w której formuje się wyrób, umieszcza się w stalowym gnieździe. Aby nadać odpowiedni kształt powierzchni wewnętrznej wyrobu, przygotowuje się wzornik wykonany z blachy stalowej. jest on zamocowany na dźwigni umożliwiającej przysuwanie i odsuwanie go od formowanego wyrobu w płaszczyźnie pionowej i poziomej. Masę formierską przeznaczoną do toczków ręcznych przygotowuje się w formie walców lub galet. W zależności od głębokości wyrobu formuje się ją wstępnie jako kulkę lub liść. Masa powinna być należycie odpowietrzona i mieć wilgotność około 22%.
Usunięcie pęcherzyków powietrza z masy zwiększa jej plastyczność i wytrzymałość mechaniczną w stanie surowym, zmniejsza porowatość po wypaleniu, a także zmniejsza ilość defektów w strukturze czerepu, objawiających się jako pęknięcia po wysuszeniu lub wypale. Formierz uruchamia toczek, urywa z walca miękką masę i formuje kulkę, którą wrzuca w środek wirującej formy gipsowej. Następnie stopniowo opuszcza dźwignię toczka z wzornikiem. Po oparciu się wzornika o masę przyciska lekko dźwignię wrzeciona w dół oraz do boku formy, aż do oporu, i wtedy wzornik rozprowadza masę oraz wyciska ją w kierunku pionowym ku górze. Następnie formierz unosi wzornik do pozycji wyjściowej. Zdejmuje nadmiar masy i ponownie opuszcza wzornik w celu ostatecznego nadania wyrobowi kształtu wewnętrznego i przy okazji jego wygładzenia. Obrzeże wyrobu odcina się za pomocą harfy z drutem tnącym. Po zatrzymaniu gniazda formę z wyrobem w środku wyjmuje się z głowicy i odstawia do suszenia.
Odlewanie
Odlewanie przedmiotów w formach gipsowych jest bardzo efektywną metodą pracy, która znajduje zastosowanie przy masowym wytwarzaniu wyrobów o bardziej złożonych kształtach, o cieńszych ściankach i dużych rozmiarach oraz takich, które wymagałyby żmudnej pracy i wielkiej rzemieślniczej sprawności do ich wykonania. Przed rozpoczęciem procesu odlewania formy gipsowe muszą zostać odpowiednio przygotowane. Przede wszystkim powinny być dobrze wyczyszczone i suche, tak aby ich powierzchnia sprzyjała nieprzywieraniu materiału ceramicznego. Jeżeli forma składa się z kilku elementów, powinna być w odpowiedni sposób mocno związana. Formy ustawia się nad tzw. korytkiem. Przygotowaną masę lejną, przepuszczoną przez sito, wlewa się bezpośrednio do form gipsowych powolnym, ciągłym ruchem. Po zapełnieniu form masą lejną należy ją delikatnie przemieszać.
Woda odciągana jest dzięki działaniu sił kapilarnych materiału formy, zaś na ściance formy powstaje czerep, którego grubość rośnie z czasem. Grubość tworzącej się warstwy kontroluje się wycinając z kołnierza odlewu kawałek masy. Grubość ścianek dobiera się w zależności od wielkości i kształtu asortymentu, w zakresie od 3 do 8 mm. Po wylaniu masy lejnej do korytka formy pozostawia się odwrócone do góry dnem do czasu całkowitego odcieknięcia masy. Następnie ustawia się je z powrotem w pozycji wyjściowej i czeka na stwardnienie masy. Wówczas można przystąpić do otworzenia formy i wyjęcia półfabrykatu. Po jego wyjęciu, wysuszeniu oraz obróbce szwów i zamyciu produkt jest kierowany do pierwszego wypału biskwitowego.
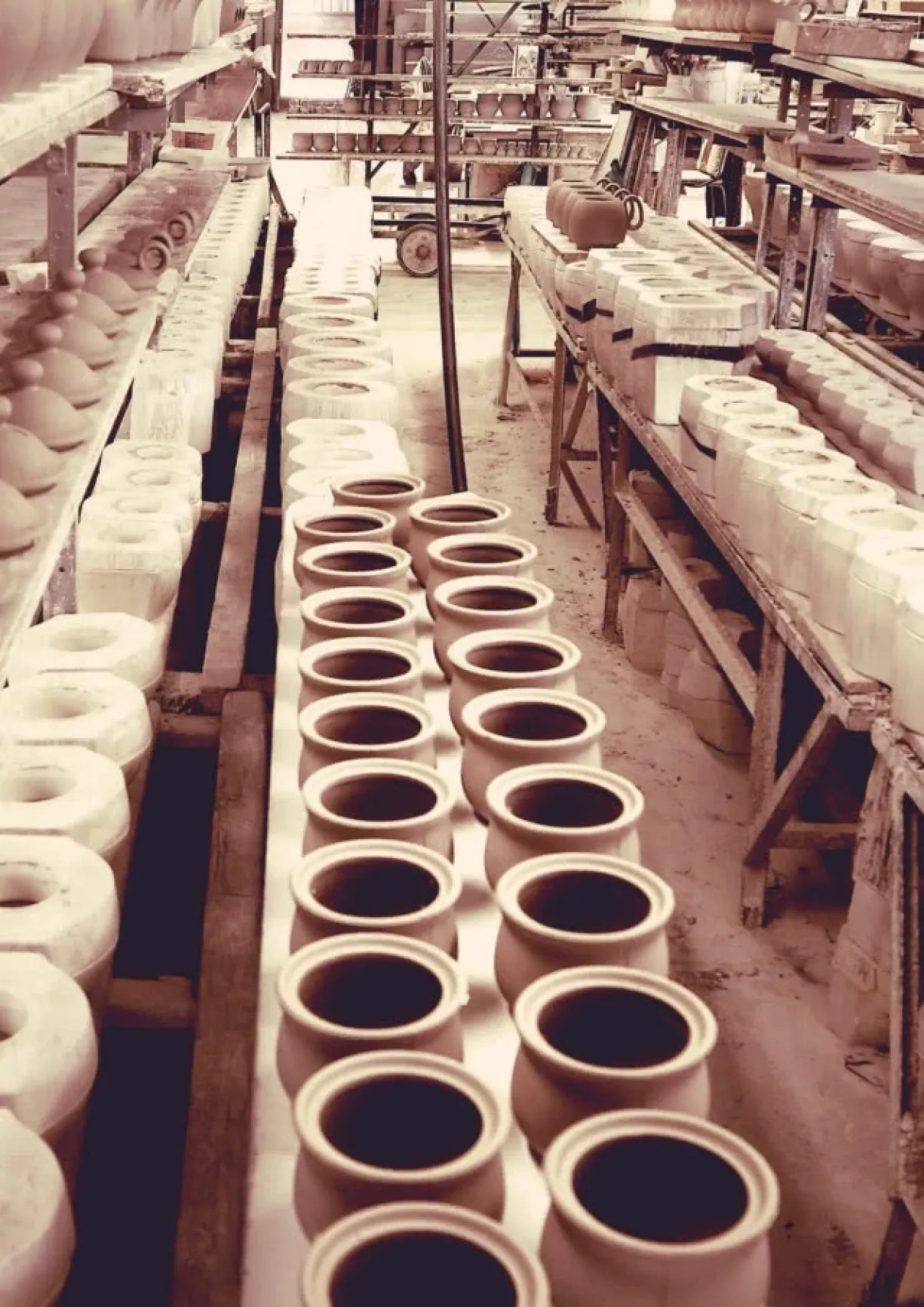
Dekorowanie
Jedną z najbardziej interesujących i znaczących, szczególnie dla Manufaktury, ręcznych technik pracy z wyrobami kamionkowymi jest ich zdobienie metodą stempelkową — zajęcie wymagające zdolności i umiejętności. Dobry zdobnik musi zdobywać doświadczenie latami. Dekorację nanosi się na każdy wyrób za pomocą stempla maczanego w odpowiednich farbach ceramicznych, które utrwalane są później w piecu podczas wypału ostrego (w temp. 1200°C). Dekoracje muszą być nanoszone według wyznaczonego wzoru i według ustalonych zasad, a mimo to każdy powstały produkt jest indywidualną, niepowtarzalną formą. Tutaj „błąd” ludzki jest cennym przejawem uprawiania rzemiosła artystycznego. Półprodukt, tak zwany biskwit, czyli produkt ceramiczny po pierwszym wypale w temp. 850°C, trafia na stół malarki. Malarka oczyszcza wyrób z pyłów za pomocą wilgotnej gąbki. Ustawia go na małym ręcznym toczku, co ułatwia obracanie przedmiotu w trakcie malowania. Następnie, używając przygotowanych wcześniej lekko wilgotnych stempli i mocząc je w odpowiednio dobranej farbie ceramicznej, nanosi na półfabrykat dekorację według określonego wzoru.
Do wykonania samych stempli wykorzystuje się gęste gąbki tapicerskie, które są łatwe i tanie w obróbce, choć bardzo szybko się zużywają i podlegają degradacji. Wzory stempli przygotowuje się obecnie w programach graficznych 2D i wycina na ploterze, co pozwala podnieść stopień ich skomplikowania i utrzymać ich jakość na odpowiednim poziomie.
Malarka zdobi naczynie, dostosowując układ i kompozycję stempli do jego kształtu. Musi przy tym znać dokładnie podziały wzorów istniejących w katalogach zakładu i wiedzieć, w jaki sposób rozłożyć dany wzór na różniących się kształtem i wielkością produktach. Przy tak bogatym asortymencie kształtów i wzorów, jaki posiada fabryka (obecnie ponad 700 kształtów i tyle samo wzorów), nie jest możliwe zapamiętanie przez malarkę każdej z tych kombinacji. Dlatego stworzono bazę zdjęć z gotowymi wyrobami, w której system — po wpisaniu odpowiednich kodów — pozwala odnaleźć określoną kombinację kształtu i wzoru. Warto tutaj podkreślić, iż zatrudnione w fabryce osoby wykonują swą pracę w systemie akordowym, dlatego też czas poświęcony na pojedynczą czynność odgrywa dla nich bardzo istotną rolę. Stąd usprawnienia i wspomaganie pracy przy użyciu nowych technologii. Dekoracje w Manufakturze zostały podzielone na trzy kategorie wg stopnia trudności: wzory tradycyjne (w slangu zakładowym „tradycja” lub „podstawówka”), wzory unikatowe i wzory superunikatowe, Klasyfikacja ta opiera się na stopniu trudności malowania danego wzoru, wynikającym z liczby użytych kolorów, liczby i kształtu użytych stempli oraz czasu, jaki (mniej więcej) jest potrzebny do wymalowania danego wyrobu. Klasyfikacja determinuje ostateczną cenę produktu, dlatego często ten sam kształt wymalowany w różnych dekoracjach będzie miał różną wartość rynkową.
Większość stałych kontrahentów Manufaktury zamawia wzory tradycyjne — wciąż największe zainteresowanie, szczególnie na rynku amerykańskim, wywołują najlepiej rozpoznawalne dekoracje kobaltowe. Część wzorów tradycyjnych oferowanych przez Manufakturę to tak zwane wzory „muzealne”, oparte na zdobinach przedwojennych, które są stosowane przez wszystkie firmy na terenie Bolesławca. Dlatego klasyczne „kropki” możemy zakupić u każdego z producentów bolesławieckiej kamionki.
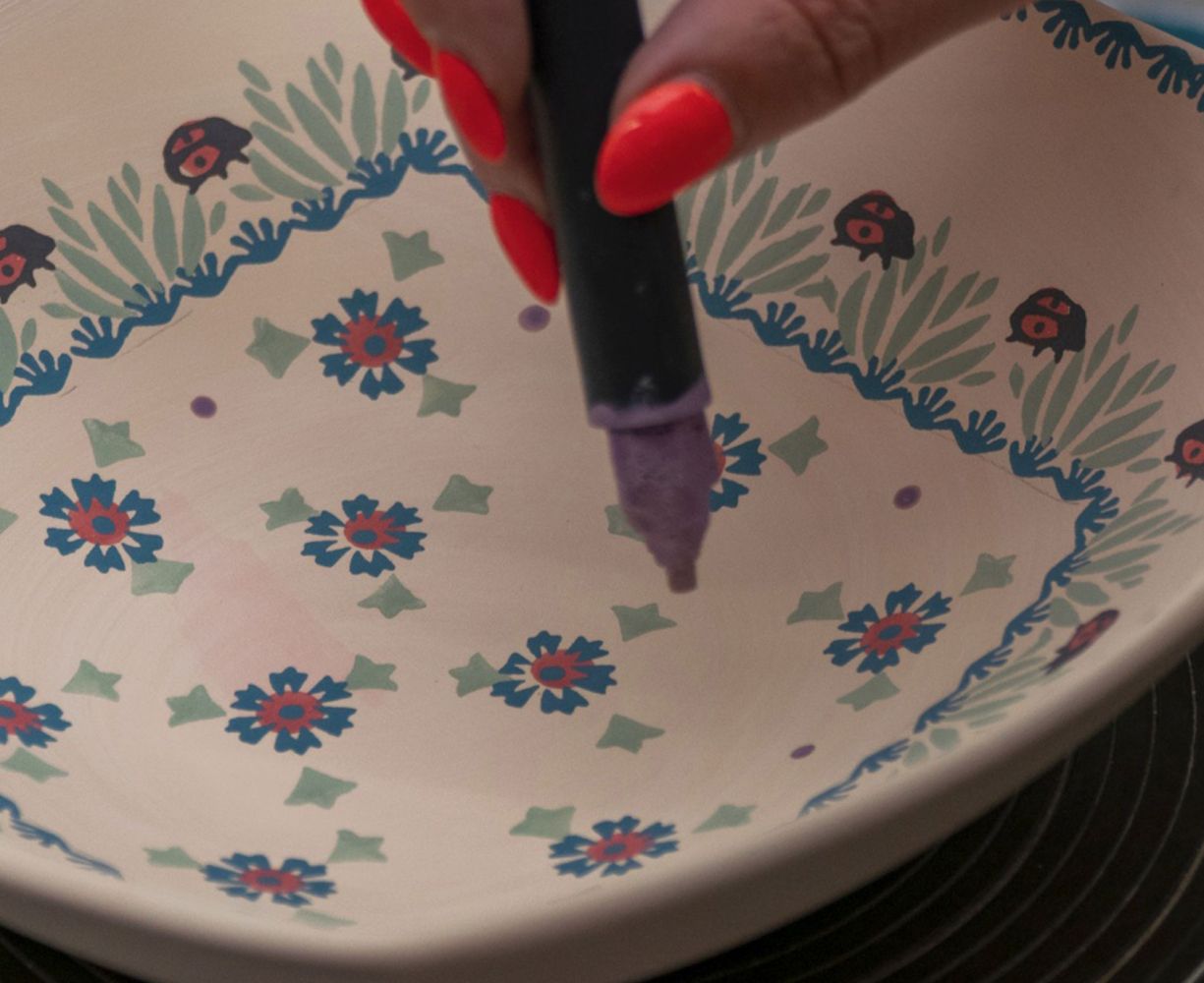
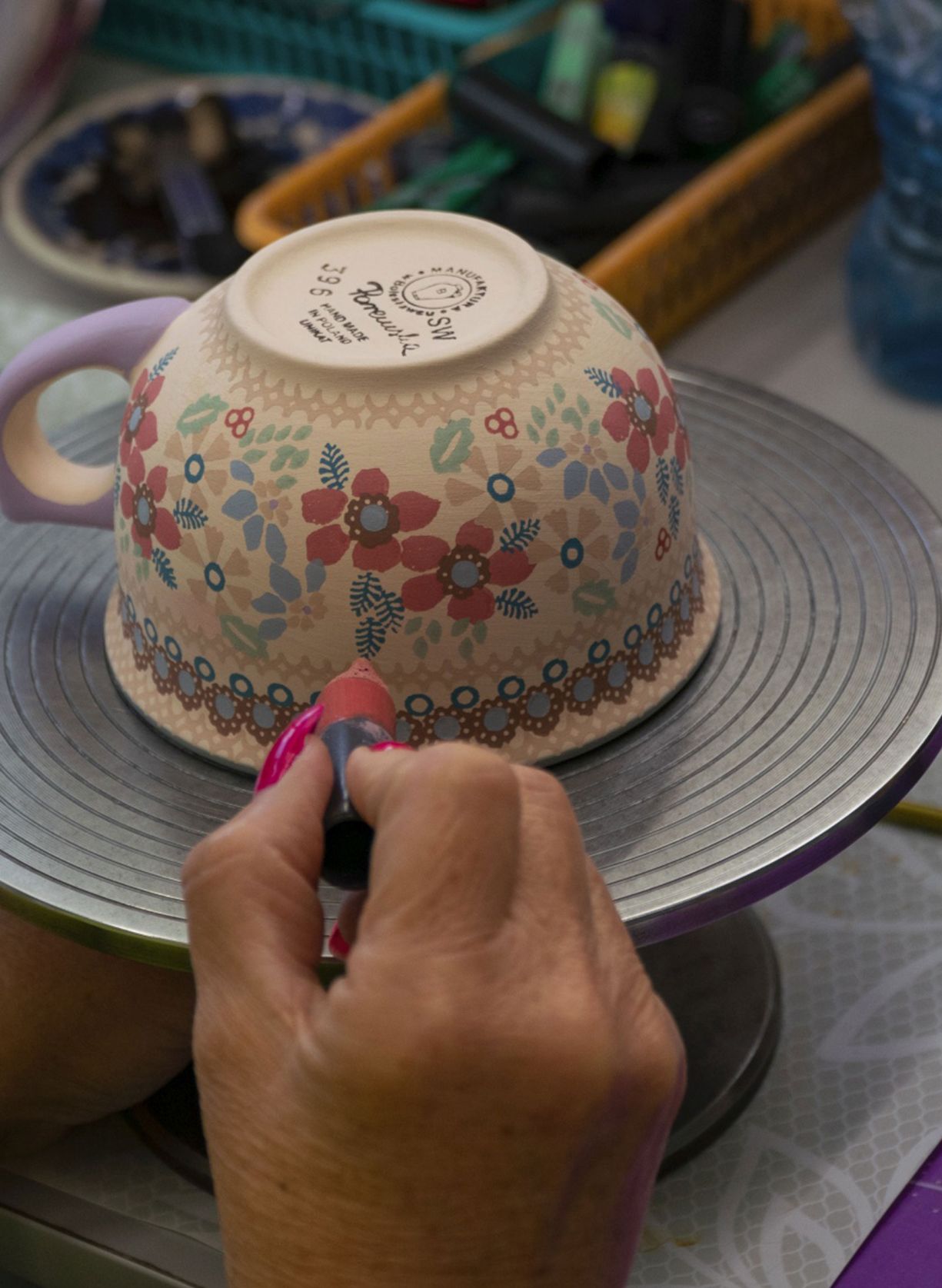
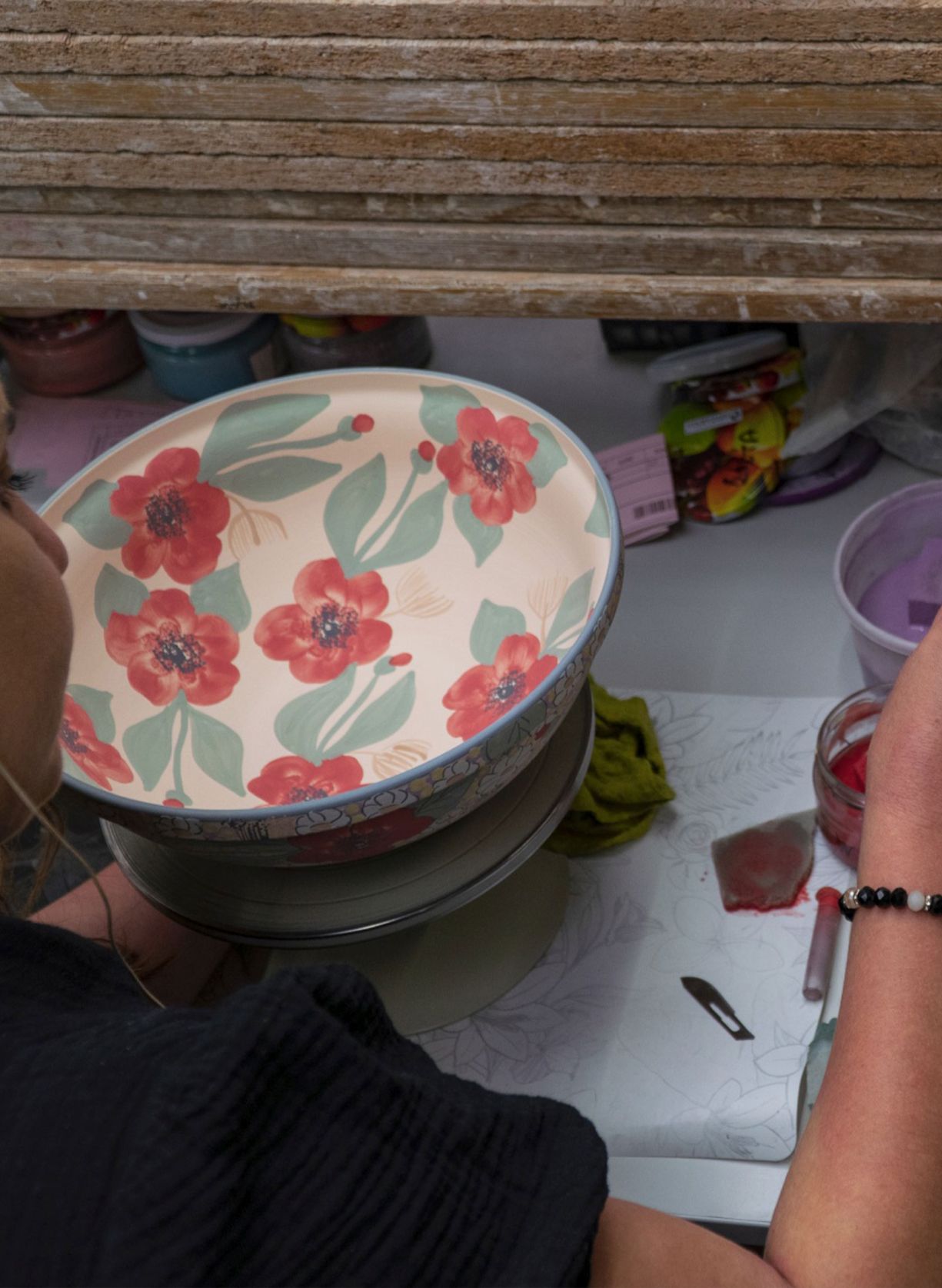
Warto podkreślić, iż z trzech powyższych procesów to właśnie dekorowanie jest najbardziej angażujące i najlepiej obrazuje indywidualny charakter wyrobów. Mimo narzuconych norm i określonych zasad dekorowania każda malarka zachowuje swój unikatowy styl, dlatego czasem zaprasza się dekoratorki do podjęcia wyzwania i stworzenia nowych projektów na bazie własnych spostrzeżeń, doświadczeń i umiejętności. Podpis osoby malującej dany wzór podkreśla unikatowy charakter produktu i pozwala dostrzec pewien indywidualizm i styl.
Należy zdać sobie sprawę, iż wszystkie powyższe procesy angażują człowieka, wykorzystując jego ręce jako narzędzie pracy, czasem też korzystając z jego zdolności twórczych. Procesy te są w pewnym sensie odtwórcze, przebiegają bowiem według wcześniej założonych norm i ustaleń, wypływających z koncepcji projektowych. Rzemieślnik balansuje zatem niejako na granicy, będąc jednocześnie projektantem i częścią „systemu produkcyjnego”. Jednak każde z tych działań wymaga konkretnych umiejętności, a przede wszystkim — doświadczenia.
O wiele cenniejszy jest pracownik, który pozyskał stosowną wiedzę o wytwarzaniu półproduktu na danym etapie, niż osoba nowo zatrudniona, przed którą długa droga do opanowania pewnych umiejętności i dostosowania się do rytmu produkcji. Ten rytm wciąż oparty jest na indywidualnej pracy ludzkich rąk, co ma ogromny wpływ na proces projektowy i całościowe myślenie o produkcie.
Dostosowanie kolejnych etapów wdrożeniowych musi być podparte wiedzą technologiczną, ale przede wszystkim należy w tym procesie uwzględnić tak zwany „błąd ludzki”, a często (jak w przypadku dekorowania) umieć wykorzystać go w taki sposób, by stał się atutem, a nie problemem. Zachowanie tradycyjnych metod w produkcji, a jednocześnie podążanie za trendami i podejmowanie prób ich kreowania to tandem, który pozwala mocno odróżnić się od konkurencji i dojrzale wpływać na umacnianie wizerunku firmy na rynku.
Powyższe techniki to jeden z głównych elementów procesu projektowego. W głowie projektanta rodzi się wiele pomysłów, wyjątkowych, unikatowych, autorskich. Problem zaczyna pojawiać się przy założeniach produkowania danych kształtów w większej ilości. Największym wyzwaniem staje się wówczas znalezienie consensusu, złotego środka — punktów stycznych dla idei projektowej i wymogów produkcyjnych w zbiorze zawierającym wiele elementów: wiele możliwości i idących za nimi rozmaitych efektów.